Em uma corrida de carros, a parada para reparos no pit stop precisa ser rápida para que o veículo retorne o quanto antes para o grande prêmio. E, na disputa entre ofertar um bom serviço para o passageiro e equilibrar as contas de operação, um trem precisa ter o menor tempo possível fora da ferrovia, sejam em serviços urbanos, regionais ou de alta velocidade. E se aplicássemos esse conceito do pit stop para a manutenção ferroviária aliando inteligência artificial?
A malha ferroviária alemã conta com mais de 30 mil quilômetros, divididos entre serviços urbanos, regionais e de alta velocidade. Somente a DB (Deutsche Bahn), de propriedade do Estado alemão, transporta 7,6 milhões de passageiros por dia. Isso significa que o processo de manutenção desse sistema é vital para o funcionamento dos serviços.
A Siemens é o maior conglomerado industrial da Alemanha e tem uma atuação expressiva no mercado internacional de ferrovias. Um de seus centros de manutenção ferroviária fica em Dortmund, no oeste da Alemanha. Conta com uma área total de 70.000 m² e 5,5 km de trilhos, operando 24 horas por dia. Este local foi criado para revolucionar os processos e fluxos de trabalho de manutenção. Conta com 6 vias, duas delas reservadas para trens de alta velocidade. Atualmente esse local se encontra em expansão e nos próximos anos chegará a 87.550 m², aumentando sua capacidade de atendimento, que hoje é para 84 composições.
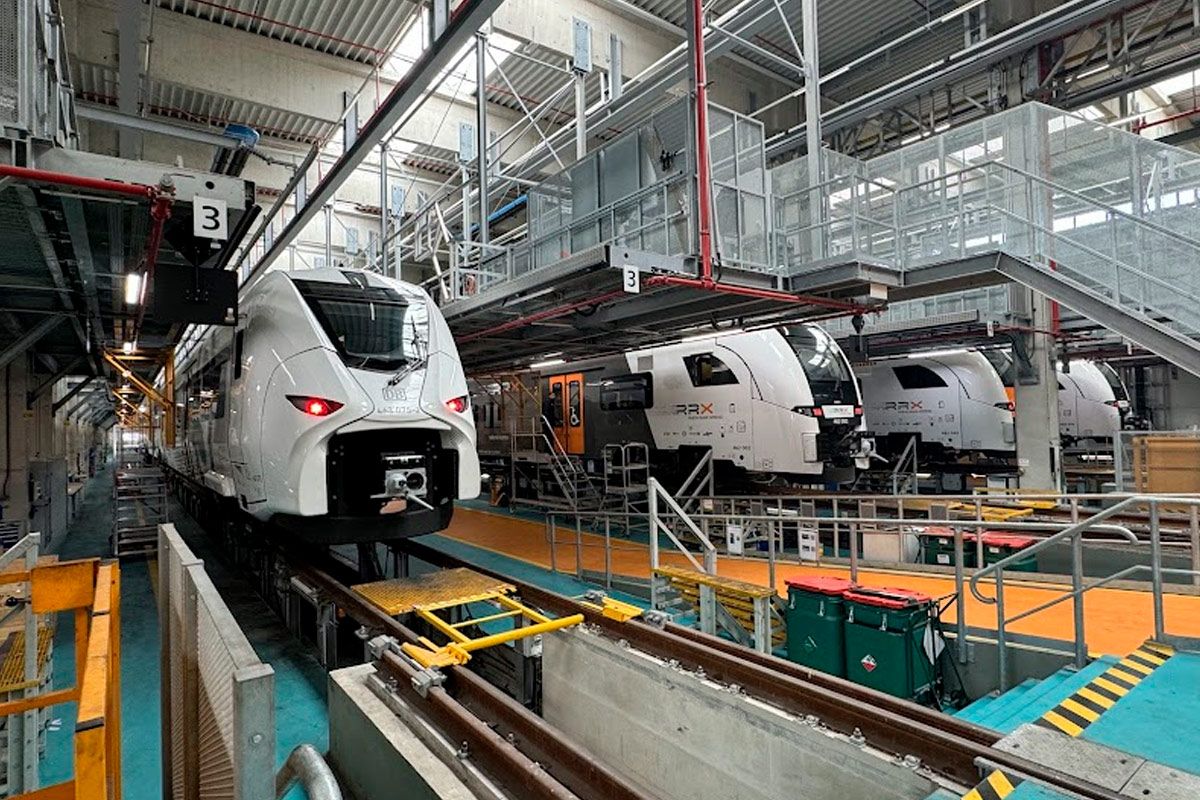
Nesse centro de manutenção não há papel mediando os trabalhos e tudo é pensado e estruturado nos chamados processos End-To-End, uma cadeia de processos integrados com o objetivo de entregar uma solução ágil e funcional aliada a diferentes tecnologias. A empresa é clara ao falar sobre este local: “Não se trata de um depósito para manutenção de trens”. Todo o processo é digital, e o uso de APIs – conjuntos de ferramentas que integram aplicações de software – tem o objetivo de alcançar 100% de disponibilidade da frota para a operação.
Um centro de manutenção que foge à regra
Até então, o processo de manutenção ferroviária ocorria com o controle das quilometragens das composições e com paradas na oficina programadas para os reparos. Em outras palavras, o trem é retirado de circulação, levado ao pátio e aguarda as peças de reposição e seu reparo antes de voltar ao sistema. Há ainda casos mais críticos, quando a composição precisa de reparos emergenciais devido a uma falha inesperada ou algo descoberto no próprio pátio de manutenção. Dependendo do problema, o trem pode ter que esperar por dias ou meses antes de retornar aos trabalhos.
Neste novo centro, o processo começa de forma diferente. O próprio trem possui um ciclo de análise de seu funcionamento e conta com armazenamento de dados sobre eventuais falhas em diferentes âmbitos (desde o tempo de abertura e fechamento das portas, até o monitoramento de seu peso e sistemas de suspensão). Essas composições são capazes de avisar o centro de manutenção sobre sua condição de operação antes mesmo de chegarem ao pátio. Isso muda tudo.
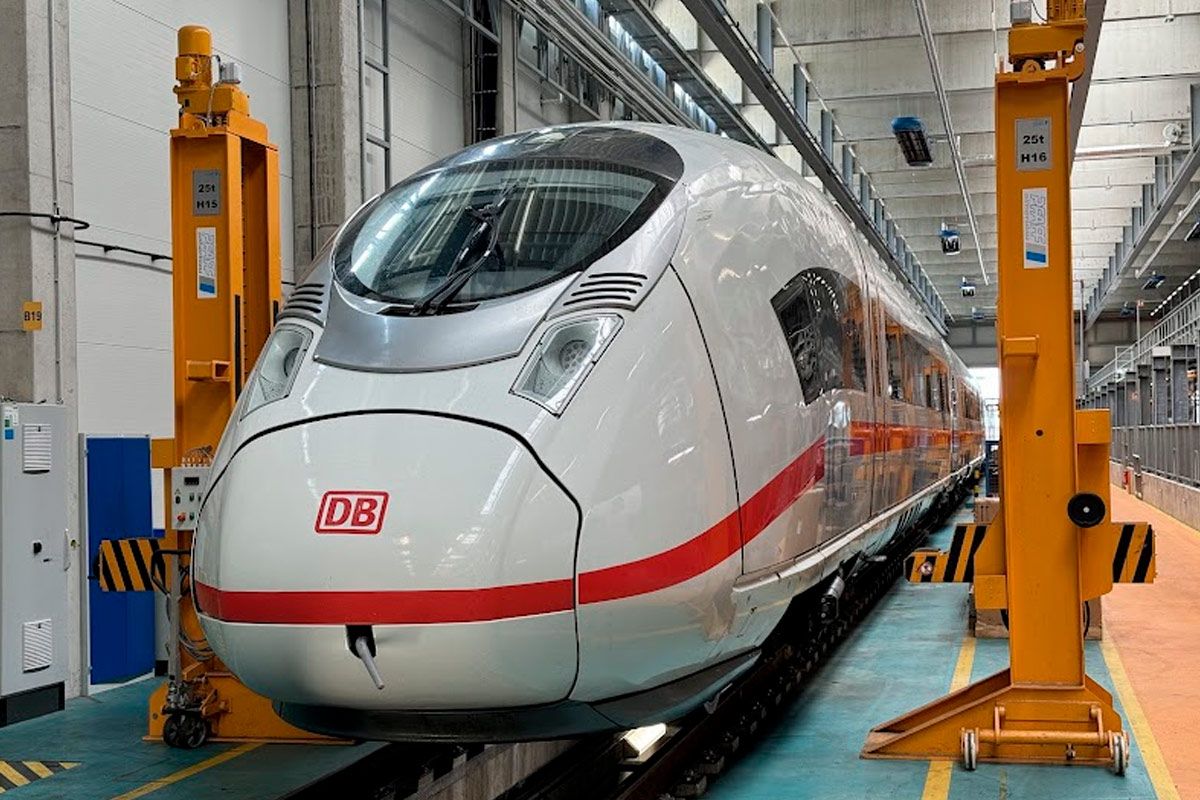
Cada trem suburbano é capaz de armazenar 120 MB de dados por dia, ou 3 GB por mês. Já comboios de alta velocidade armazenam 1.2 GB por dia, ou 30 GB por mês. Esse montante de dados tem um objetivo claro: abastecer as alças de análise e tomada de decisão baseadas em inteligência artificial modeladas para otimizar o desempenho de todo o sistema ferroviário.
Um dos segredos para que os veículos fiquem o menor tempo possível parados é uma impressora 3D, instalada no próprio galpão da Siemens, que fabrica as peças de reposição necessárias. Assim, o trem recebe os reparos assim que chega, como em um pit stop de fórmula 1, e volta rapidamente para a ferrovia. A máquina ainda pode produzir peças para outros sistemas necessários à operação e entregá-las em 24 horas. Além desse equipamento, o centro possui uma via dedicada à limpeza dos trens, que dura entre 20 e 40 minutos. A impressora local é somente uma na cadeia integrada de 40 máquinas espalhadas em diferentes centros da Siemens, atuando de forma conectada para a solução de demandas.
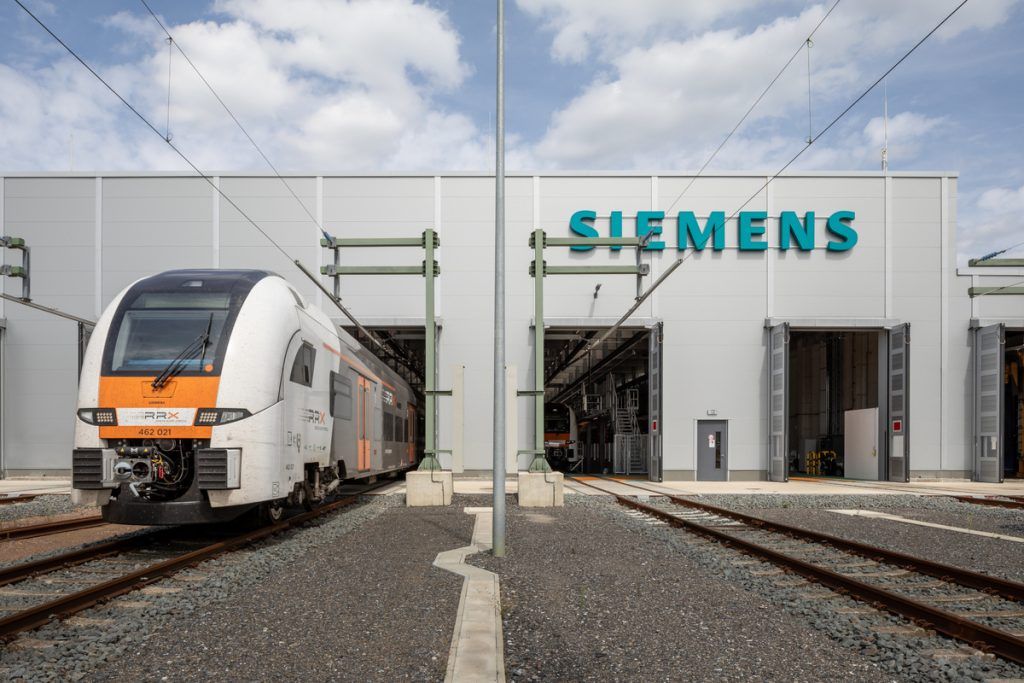
Uma curiosidade é dada pelo fato de que muitos equipamentos utilizados na manutenção se comunicam via Wi-Fi. O centro de manutenção é extremamente limpo, bem iluminado e conta com diferentes tipos de scanners e câmeras que checam o trem desde sua entrada, permanência e retorno à operação.
Clones de trens
Ainda que trens sejam fabricados em série, às vezes com 50 ou 100 unidades do mesmo modelo, nem sempre uma unidade se comporta como a outra. Então, com base nos dados da operação e nas visitas ao centro de manutenção, a inteligência artificial cria uma espécie de clone virtual do trem, e os algoritmos preveem futuras falhas. É o chamado “gêmeo-virtual”, capaz de antever falhas. Esse clone é modelado para que possa comparar o trem em diferentes momentos da manutenção e, ainda, em datas futuras – proporcionando um histórico da evolução das composições. A tecnologia faz com que sejam reduzidas em 30% as paradas desnecessárias no pátio de manutenção.
A União Europeia enxerga a ferrovia como pilar fundamental na descarbonização dos sistemas de transportes, ou seja, transporte de pessoas com menos níveis de poluição. Por isso, é consenso em ampliar as ferrovias. Isso significa mais passageiros no sistema, e a necessidade de uma frota de trens mais robusta e mais disponível. É ai que entra a importância de centros de manutenção como esse que conhecemos, para que o passageiro possa ter uma viagem confortável e eficiente.
Assista o vídeo da visita ao centro em nosso canal no YouTube:
https://youtu.be/w5MBgcwN6c0